Find out more about the importance of choosing the right materials for labelling your pharmaceutical products.
When it comes to labelling your pharmaceutical product, there are two key factors you need to consider. The first is making sure that the information you provide is accurate and printed correctly on your label.
The second is the materials used to create the label. Choosing the right material for your pharmaceutical label is essential to ensuring that the label remains durable for the lifespan of the product so that the information is always available for the consumer to access.
For example, if the product has a shelf life of 2-3 years, but the label warps, fades, or peels
in 6 months making the details regarding dosage or instructions illegible, the consumer will not be able to continue to use it.
In this blog, we explore the practical qualities a pharmaceutical label should have and the
range of available materials.
What practical qualities do pharmaceutical labels need?
To understand which materials are best for your pharmaceutical labels, first, you need to
know what durable qualities they need.
equipment, your labels need to be able to withstand a wide range of conditions and
temperatures, including:
- Moisture/humidity and submersion
- Chemical exposure
- Rough-textured surfaces
- High and low temperatures
- UV light/radiation
Another important consideration is that the label cannot be produced from materials that could potentially contaminate your product.
What materials are best for pharmaceutical labels?
The different materials available for pharmaceutical labels include various types of polypropylene and paper stocks with matt or semi-gloss finishes. Each type can be applied with extra-strength adhesive to prevent your label from being removed easily.
Paper labels
Paper labels are one of the most commonly used label materials in the pharmaceutical industry. They offer simplicity, cost-effectiveness, and ease of printing. However, their suitability depends on the requirements of the product.
Pros
- Cost-effective for large production runs
- Compatible with a wide range of printing methods
- Suitable for products with short shelf lives where durability is less of a concern
Cons
- Susceptible to moisture, humidity and other factors that could lead to label damage
- Limited resistance to chemicals, solvents, and abrasion.
- Not ideal for products that require long-term storage or expose to harsh conditions
For these reasons, paper labels are better suited to pharmaceutical products with a short shelf life, such as over-the-count medication and disposable medical supplies.
Polypropylene
Polypropylene labels offer enhanced durability and resistance to environmental factors compared to paper labels. They are commonly used for pharmaceutical products that require extended shelf life or exposure to challenging conditions. Polypropylene labels are available in white, clear, or silver, which each has its benefits.
Pros
- Resistant to moisture, humidity, and temperature fluctuations
- Excellent chemical and solvent resistance
- Enhanced durability and abrasion resistance
- Polypropylene provides a degree of flexibility for cylindrical or curved products making it easier to apply.
Cons
- High cost compared to paper labels
- Limited compatibility with certain printing methods
Polypropylene labels are recommended for pharmaceutical products that are stored in humid or damp environments, as well as those that require exposure to chemicals or solvents. They are suitable for bottles and containers that need to withstand transportation and handling.
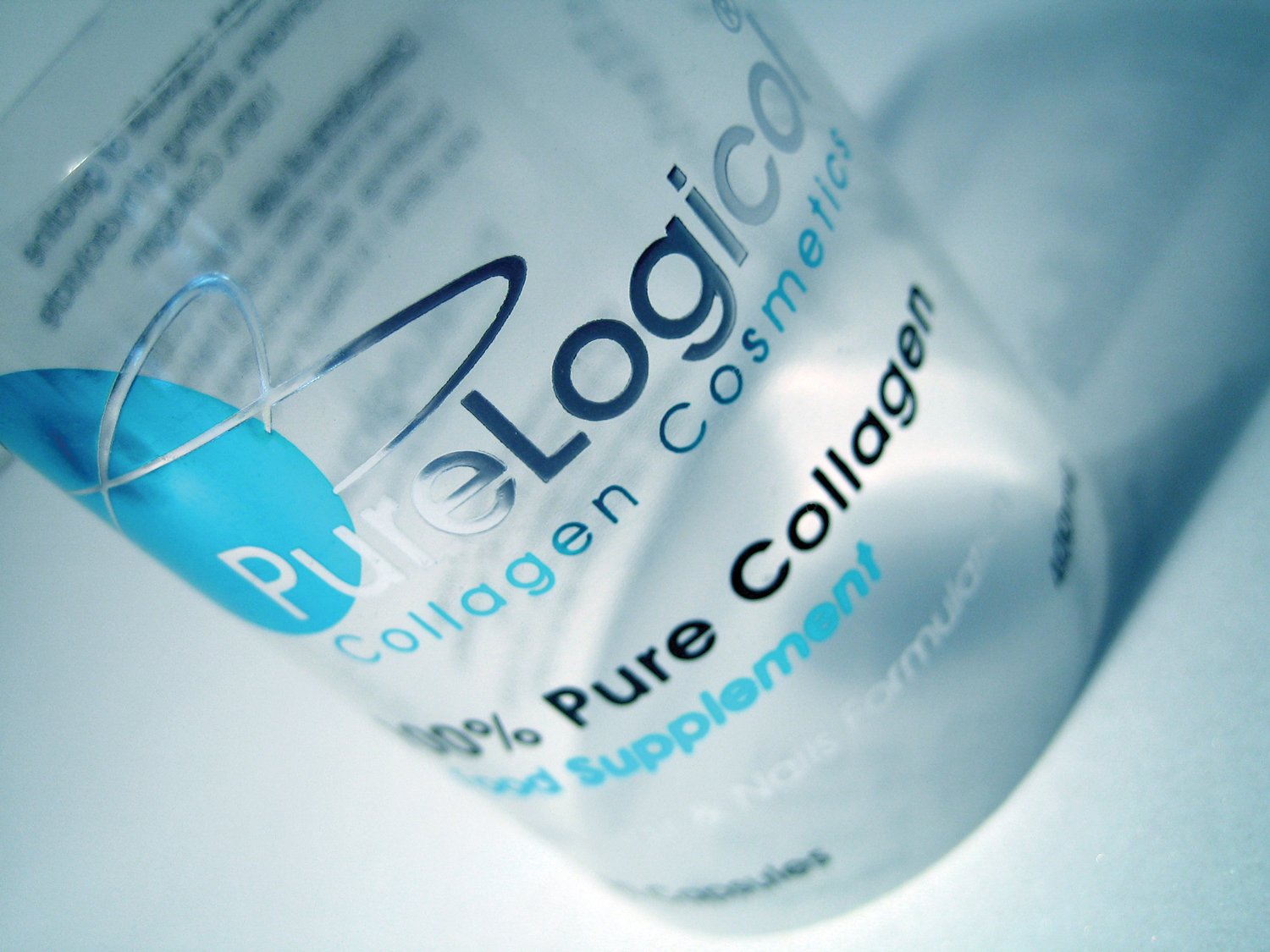
Pharmaceutical labelling services from Premier Labels
Producing regulatory-compliant pharmaceutical labels that are suitable for your product can be a time-consuming and difficult process.
That’s where Premier Labels come in.
To find out more about how we can help create the highest-quality pharmaceutical labels for your product, contact our team today, we’re on hand to help.